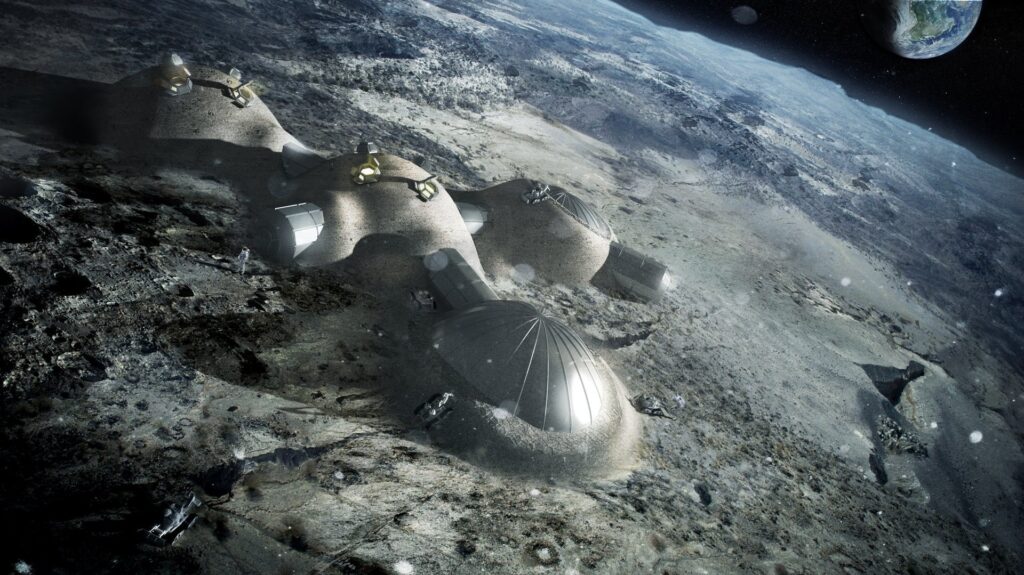
By 2028, NASA plans to make history by landing the “first woman and first person of color” on the moon as part of the Artemis III mission. This ambitious endeavor marks humanity’s return to the lunar surface for the first time since the Apollo missions concluded in 1972. With international and commercial partners, NASA aims to establish a “sustained program of lunar exploration and development,” potentially paving the way for long-term facilities and habitats on the moon.
However, the logistical challenge of transporting all necessary equipment and materials to the moon is daunting. The solution lies in utilizing local resources, a process known as in-situ resource utilization (ISRU), to construct lunar structures. This process leverages advancements in additive manufacturing (AM), or 3D printing, to convert lunar regolith into building materials. Yet, technical hurdles remain, as most 3D printing techniques are not feasible on the moon’s surface.
Innovative Approach to Lunar Construction
In a recent study posted on the arXiv preprint server, a team of researchers led by the University of Arkansas proposed an alternative method using light-based sintering to manufacture lunar bricks. This approach diverges from traditional 3D printing by focusing on creating building components rather than entire structures.
The research team, led by Wan Shou, an Assistant Professor in the Department of Mechanical Engineering at the University of Arkansas, includes Cole McCallum, Youwen Liang, and Nahid Tushar. Their collaboration extends to researchers from the University of Houston and Tampere University. The team emphasizes that the concept of a permanent lunar base has been explored since the Apollo Era, but the cost and complexity of transporting machinery and materials have always been prohibitive.
“There are many AM methods that require a solvent to prepare paste or composites for extrusion or printing; these approaches are not feasible, as transporting solvents can be very expensive,” explained Prof. Sou.
Sintering Technology: A Promising Solution
Sintering technology has emerged as a viable method for 3D printing on the moon. This process involves bombarding lunar regolith with lasers, microwaves, or other energy sources to transform it into a molten ceramic, which is then layered to form structures. However, this method is energy-intensive, potentially requiring a nuclear power source.
The team’s proposed method, known as light-based sintering, utilizes sunlight concentrated by optics to melt lunar regolith into feedstock. This technique has been tested on Earth with lunar regolith simulant to produce glass and mirrors. On the moon, solar energy is abundant, making it a reliable power source compared to alternatives that require transportation from Earth.
“Because of this, our team envisions a system where only lunar material is needed for the structures themselves, thus eliminating the bottleneck of binder resupply missions from Earth,” added Cole McCallum, the study’s first author.
Challenges and Future Directions
Despite its promise, light-based sintering faces challenges when used to create entire structures. The team found that focusing on manufacturing interlocking and reconfigurable bricks was more effective. This “Lego Bricks” approach is advantageous because it fits the volume constraints of lunar missions, as the space needed to fabricate each unit is minimal.
Their research builds on existing studies into sintering technology, including NASA’s work with the space architectural firm SINTERHAB. This collaboration proposed equipping NASA’s ATHLETE vehicle with microwave-sintering technology. However, the team’s concept stands out due to its focus on reconfigurable bricks.
“The reconfigurability of our brick assemblies is exciting because of the flexibility we can achieve with the building process,” said McCallum. “For structures where a bulk of material is needed and where high precision isn’t demanded, as in the case of radiation shielding, we feel our method holds a lot of promise.”
Next Steps in Lunar Habitat Development
Before this concept can be realized, significant research and development are required. As Shou indicates, optimizing sintering parameters and material properties is crucial. The team plans to build a prototype and conduct laboratory tests to refine and scale the technology for lunar use. They must also address how the 3D printer will navigate the lunar surface and its power requirements.
“In the future, we’ll need to consider how the sintering process changes in a vacuum, or what modifications to the build platform will be needed so that parts can be reliably made while tracking the sun,” concluded McCallum.
As NASA and its partners continue to push the boundaries of lunar exploration, the development of sustainable building methods like light-based sintering will be critical. The potential to create habitats using local resources not only reduces costs but also represents a significant step toward establishing a permanent human presence on the moon.