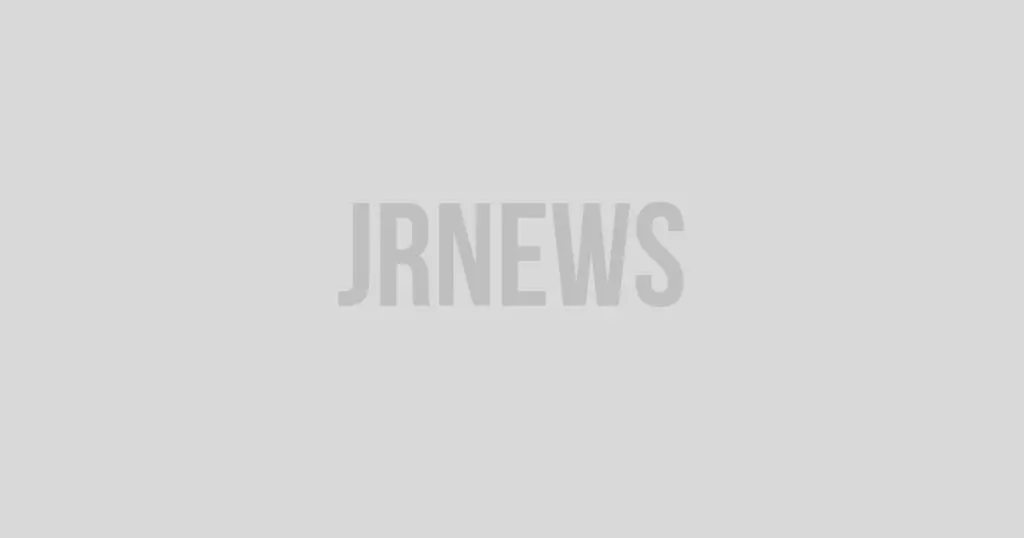
In a groundbreaking development, researchers at Penn Engineering have unveiled a method that enables swarms of tiny robots to construct complex structures without the need for blueprints. This innovative approach mimics the natural building processes of bees, ants, and termites, which rely on simple cues rather than centralized planning.
The research, published in Science Advances, demonstrates how virtual swarms can build honeycomb-like structures in computer simulations. “Though what we have done is just a first step, it is a new strategy that could ultimately lead to a new paradigm in manufacturing,” said Jordan Raney, Associate Professor in Mechanical Engineering and Applied Mechanics, and co-senior author of the study.
A New Paradigm for Building
Traditional human engineering has always depended on detailed planning, from ancient stone tools to modern space stations. Even cutting-edge technologies like 3D printing require precise instructions. However, the Penn researchers’ approach challenges this paradigm by eliminating the need for a pre-written script.
“What’s so different about our approach is that it sidesteps that entire paradigm,” explained Mark Yim, Asa Whitney Professor in MEAM and co-senior author. “There’s no pre-written script, no centralized plan. Each robot just reacts to its surroundings.”
This decentralized method allows construction to continue even if some robots fail, offering a robustness that traditional methods lack. Moreover, simultaneous operation of all robots could potentially accelerate the construction process.
Planning Behavior, Not Buildings
Drawing inspiration from nature, the researchers focused on the principle that simple, repeated behaviors can lead to complex outcomes. Unlike artificial intelligence researchers who often mimic biological processes, this team sought to understand how order can emerge without a central plan.
“What we wanted was a system where structure emerges from behavior,” said Raney. “Not because the robots know what they’re building, but because they’re following the right set of local rules.”
Finding the Right Rules
The challenge was to determine the rules that would guide the robots’ actions. The team experimented with various parameters, such as how robots should respond when encountering obstacles and the angles at which they should turn.
“The more we varied parameters like the turning angle, the more variation we got in the final structure,” noted Yim.
Interestingly, introducing a degree of disorder into the system enhanced the toughness of the resulting structures. This finding aligns with previous research by Penn Engineers, which showed that disorder in lattices can increase their resistance to cracking.
Building the Swarm in Reality
While the concept has been validated in simulations, constructing a real-world swarm of robots remains a future goal. The team plans to refine their simulations to better represent how these robots would function in practice.
“In our early models, we imagined the robots laying down material in straight lines, like a mini 3D printer,” said Yim. “But that may not be the most practical method. A better approach might be to use electrochemistry, where the robots grow metal structures around themselves.”
The successful implementation of this method will require advancements in building small, mobile robots capable of interacting with materials. However, the researchers are optimistic about the potential of their concept.
“We hope this gets people thinking in new ways about how things can be built,” said Raney. “Nature doesn’t start with a master plan; it starts with lots of small actions that come together into something bigger. Now we’re learning how to do that, too.”
This study was conducted at the University of Pennsylvania School of Engineering and Applied Science and supported by the National Science Foundation. Additional coauthors include Jiakun Lu, Xiaoheng Zhu, and Walker Gosrich, all from Penn Engineering.